Building the Future: How 3D Printing is Changing the Construction Industry
The advancement of 3D printing technology has been rapidly growing in recent years, and it’s now making its way into the real estate industry. Although the real estate industry has been slow in adopting new technologies in the past, early successes in the form of 3D-built homes have begun to pop up. In this article, we will explore the various ways that 3D printing is being used in the real estate industry, including its potential for creating affordable housing. We will, however, examine some of the challenges that need to be addressed to ensure the widespread adoption of this technology in the industry.
Table of Contents
Benefits of 3D Printing for Construction
Fast Production

The use of 3D printing in construction offers several advantages. The most significant may be the speed at which buildings can be constructed. 3D printing technology can empower builders to produce detailed and complex designs much faster, as the printer is capable of following provided digital models. Once the “print” is setup, the machine is left to deposit the material in the specified locations. Some early buildings (smaller) are being printed in a 24 hour span. This means that large-scale construction projects can be completed in a fraction of the time it would take with traditional construction methods. Once this technology gets refined, there is no reason why the printing cannot continue day or night. Imagine having a worker that would build you houses day and night with no rest! THIS is what you get with 3D printing.
Almost Zero Material Waste
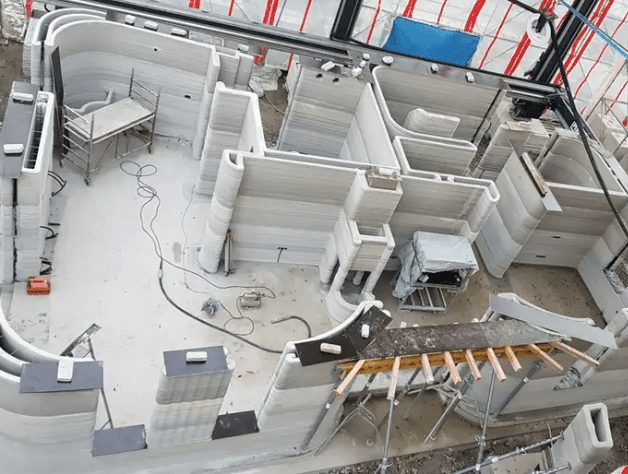
3D printing in construction has the potential to significantly reduce the amount of waste generated during the construction process. Traditional construction methods often result in a large amount of waste, with excess materials being discarded or unused. According to the National Association of Home Builders (NAHB), a 2,000 square foot home being built sends 8,000 pounds of trash to our local landfills. By 2025, it is expected to reach 2.2 billion tons (that’s 2,200,000,000 tons) of waste annually (as in every single year) according to Transparency Market Research). Using 3D printing technology can help save money on material costs. This is due to the fact that it allows for precise and efficient placement and use of materials.
The amount of waste in our current construction operations is staggering. For those who have not had a home built recently, it is clear that a cost analysis between efficient use of materials and labor costs has been carried out. Laborers will make very little effort to reuse scraps, opting the quick/easy task of just cutting up a full board instead. Overall, the reduction of waste is a key advantage of using 3D printing technology in construction.
Cost-Effectiveness
3D printing technology allows for less material usage and involves fewer people working on the construction, which results in significant cost savings. The technology also reduces supply costs, and faster building means more money saved. For jobs that are lost in manual labor of placing blocks or laying bricks, employees are utilized to maintain the pumps and equipment that are providing the build. The lesser desirable jobs will be filled by the robots, which will require additional staff to operate and maintain.
Endless and Innovative Design

Another benefit of using 3D printing in construction is innovative design solutions. 3D technologies can improve project planning as they can be used already at the design stage. Starting from CAD plans of the buildings, which are technical drawings with all the parameters, 3D construction models can be made to meet clients’ expectations and show them the best design solutions. Additive manufacturing can help address clients’ issues and present correct answers to their questions.
Our construction presently is almost solely straight lines and fairly boring architecture. These lines are due to the clear limitations of the materials used. In 3D printing, however, we can dream up any shape of walls we want. Moving a wall in a design is as simple as using a CAD program, which means we can design and re-design quickly and easily.
One of the main advantages of 3D printing is its ability to quickly and accurately create models of buildings and structures. This allows architects, engineers, and builders to visualize and test designs before they are built, saving time and money on the construction process. 3D printing also makes it easier to create custom designs and unique features that may be difficult or impossible to achieve with traditional building methods. Traditional construction methods often require a significant amount of time and resources to create intricate designs and shapes.
Tired of straight and boring walls? 3D printing makes that no longer the case. You can (literally) print out any size and shape element you want. In conventional structure, our materials and installation methods are most conducive to straight lines. These limits do not apply to 3D printing.
Marketing and Sales Improvement

In addition to the engineering applications, 3D printing is also being used to create models of furniture, fixtures, and other interior design elements. This allows builders and designers to create virtual walkthroughs of properties and give potential buyers a better sense of the space before it is built. This can also be used in the construction process to check for potential design errors before the construction process begins and avoid costly errors during the construction process.
These virtual models also have the potential to revolutionize the way we buy and sell real estate. For example, virtual walkthroughs and 3D models of properties can be easily shared online, making it easier for buyers to view properties from anywhere in the world. This could greatly increase the number of potential buyers for a property and make it easier for sellers to find the right buyer.
Imagine putting on a pair of virtual reality goggles, and “walking” in your future home before it’s ever built! Want to move that wall over a few inches? Done. Remove a wall, or make one wavy or curved? Done! You can make endless changes, and see the 3-dimensional representation of it before your eyes before any construction ever occurs. Even when you tour a model home, you must “visualize” any changes you anticipate making. In this new/future world, you can change the color, texture, height, width, size, material all with clicks of a mouse.

Improved Safety
According to Data Bulletin, construction is one of the most dangerous professions in the United States. The use of 3D printing in construction can lead to improved safety on construction sites. This is because the technology allows for robots to be used to perform certain tasks that would have been done by human workers in traditional construction methods. By utilizing robots, human workers can be kept away from potentially dangerous tasks, reducing the risk of accidents and injuries. This can also lead to increased efficiency and productivity on the construction site, as the robots can work around the clock without the need for breaks or rest periods. Imagine the injuries that would develop if we made our home builders work a 24 hour shift! . Overall, the use of 3D printing and robotics in construction has the potential to greatly improve the safety of workers and reduce the risk of accidents and injuries on the job site.
Costs (Not now, But in the Future)
Another potential application for 3D printing in the real estate industry is the creation of affordable housing. 3D printing technology has the potential to greatly reduce the cost of building materials and labor, making it possible to build houses at a much lower cost than traditional methods. This could have a major impact on the housing market, making it possible for more people to own their own homes. This (unfortunately) is not quite the reality of the situation. The cost of the equipment is elevated because the industry is young and the initial stakeholders are billing higher fees to recuperate their R&D expenditures. As the industry becomes more mainstream, there will be more companies in the mix, and competition will lead to better consumer pricing.
Further, once we have multiple options of materials to print, the dependence on any one will lessen and allow the pricing to come down.
Drawbacks to 3D Printing in Construction
Costs (Currently)
One of the biggest drawbacks of 3D printing in construction is the high initial cost. The technology required for 3D printing is expensive and requires a significant investment. This cost may be prohibitive for some construction companies, especially smaller ones.
Presently additional costs are also required in the pursuit of permission to build. Many municipalities have not yet experienced 3D printing, and are requiring advanced proof of concept tests to verify the buildings operate in accordance with Building Code requirements. As these municipalities experience 3D printing, we expect these barriers to come down.
This can make it difficult for small and medium-sized builders and developers to adopt the technology. Additionally, there are also concerns about the environmental impact of 3D printing, as some materials used in the process can be harmful to the environment (concrete).
Concrete is considered environmentally unfriendly for several reasons. Firstly, it requires a significant amount of energy to produce, and this energy is typically derived from non-renewable sources such as coal or natural gas. This contributes to greenhouse gas emissions and global warming. Secondly, the production of cement, which is a key component of concrete, results in significant amounts of carbon dioxide emissions. The mining and extraction of raw materials used in concrete production, such as sand and gravel, can cause environmental degradation and habitat destruction.
One primary, however, disadvantage of 3D printing in construction is the high initial cost associated with the technology. The advanced technology required for 3D printing is often expensive and can require a significant initial investment. This initial cost may be prohibitive for smaller construction companies, making it difficult for them to adopt the technology. Additionally, ongoing maintenance and repair costs can also add up over time, further increasing the overall cost of implementing 3D printing technology in construction.
The cost of 3D printers capable of building houses varies widely depending on the size, technology, and capabilities of the printer. Currently, large-scale 3D printers designed for construction can cost anywhere from tens of thousands to hundreds of thousands of dollars. For example, the COBOD BOD2, one of the largest 3D printers used for construction, has a starting price of around $350,000. However, as the technology continues to advance and become more mainstream, it is expected that the cost of 3D printers will decrease over time.
Limited Material Options
Although 3D printing has made significant progress in recent years, the range of materials that can be used for construction is still limited. Currently, the most commonly used material for 3D printing in construction is concrete. However, there are other materials such as steel and glass that may be more suitable for specific projects but are not yet widely available for construction purposes. This limitation can hinder the versatility and flexibility of 3D printing in construction. Further research and development is needed to explore new materials that can be used in 3D printing for construction. This will help expand the range of possibilities and applications for 3D printing in construction and address the limitations that currently exist. It will similarly ensure that the pricing of any individual material will not spike when 3D printing technology takes hold.
Quality Control Challenges
One of the challenges of 3D printing in construction is maintaining quality control. The layer-by-layer process of 3D printing can make it difficult to detect defects or inconsistencies in the finished product. Unlike traditional construction methods where visual inspection can be done at every stage, 3D printed structures may require additional testing and inspection to ensure they meet safety and quality standards. Furthermore, as 3D printing is a relatively new technology in the construction industry, there is a lack of established quality control standards and protocols, which can further complicate the process. As a result, construction companies using 3D printing technology will need to invest in additional testing and inspection procedures to ensure the quality and safety of their structures.
Utility Routing
One of the main issues that efforts are being made to mitigate is the routing of the various required utilities. Having ability to run electrical wires, plumbing supply/drain lines and other required utilities requires advanced consideration. We can certainly drill into the 3D printed materials, but accessing some of the spaces after construction can be difficult. Finding ways to integrate utilities into the design will lead to a more efficient structure in the end.
Legal or Regulatory Issues
There are several regulatory and legal issues associated with 3D printing in construction. One of the main issues is that building codes and regulations may not yet fully address 3D printing technology. This could lead to delays or complications in obtaining necessary permits and approvals, as there may be questions about the safety and quality of 3D-printed structures. Additionally, liability concerns may arise if a 3D-printed structure fails or collapses. In the event of a failure, it may be difficult to determine who is responsible, particularly if the failure is due to a defect in the 3D printing design, installation or materials used. This highlights the need for clear guidelines and regulations for 3D printing in construction, to ensure the safety and quality of the finished product and to provide clarity for all parties involved.
Regulatory and Legal Issues
Finally, there are regulatory and legal issues associated with 3D printing in construction. Building codes and regulations may not yet fully address 3D printing technology, which could lead to delays or complications in obtaining necessary permits and approvals. Additionally, liability concerns may arise if a 3D-printed structure fails or collapses.
As the method becomes more mainstream, and has more of a track record of success or failure, this may not be a pressing issue.
What to Expect in the Future
Looking to the future, there is no doubt that 3D printing will continue to advance and improve. As the technology becomes more widely used, it is expected that the costs associated with 3D printing a house will decrease, making it a more accessible option for homeowners and construction companies. Additionally, the range of materials that can be used in 3D printing is expected to expand, allowing for even greater flexibility in design and construction. Companies are currently experimenting with an array of printing materials. We currently have successfully built with various plastics, metals, concrete, wood-plastic composites, cross-laminated timber, and ceramics/clays. Experimental printing with foams in an effort to create formwork for casting concrete is also underway. As we experiment with materials, we will find a material that provides the require strength properties, but also allows flexibility to be installed and operate in a manner that is predictable and repeatable.
As more research is conducted and regulations are put in place, it is likely that 3D printing will become a more common method of home construction, paving the way for a more sustainable and efficient future in the real estate industry.
Conclusion
Is 3D Printing the Future of Construction?
While 3D printing is still in the early stages of development in the construction industry, it has already shown promise as a viable alternative to traditional construction techniques. With the technology’s benefits, including fast production, almost zero material waste, cost-effectiveness, and innovative design solutions, it’s easy to see why it has become an increasingly popular option.
Several 3D printing construction projects have already been successfully completed. However, despite the successful projects, there are still limitations that need to be overcome. Time will tell if and when this becomes the gold standard in construction.
In conclusion, the use of 3D printing technology in the real estate industry has the potential to revolutionize the way we build, design, and sell properties. The benefits of 3D printing include cost savings, custom designs, fast and accurate model creation, and the creation of affordable housing. However, there are also challenges that need to be overcome, such as the high cost of 3D printers and printing materials, and environmental concerns. As the technology continues to improve and become more accessible, it’s likely that more companies and individuals will adopt this technology. The real estate industry needs to keep an eye on the latest developments in 3D printing and consider how it can be integrated into their operations. This will allow them to stay competitive and meet the demands of their customers.
In the end, Red Flag is convinced that 3D Printing will change the way we build homes. What are your thoughts? Comment below